Warehouses are bustling spaces filled with potential safety risks. That’s why it’s never a bad idea to minimise risk by regularly reviewing the effectiveness of your warehouse safety plan.
A few interesting facts – 90% of forklift drivers get into an accident sooner or later. Slips, trips, falls and handling injuries are the most common in warehouses – most of the time, these events are preventable.
Before we dive in, please note that we are not Safety professionals, this post was informed by thorough online research – always consult a Safety expert if you’re looking for specifics.
So, are you ready to double down on your commitment to a safer workplace?
Let’s get started.
Why Are Some Warehouses Safer Than Others?
It’s good practice to compare those who get it right and those who don’t. OSHA jumped the gun by providing this insightful list of the common denominators of an unsafe depot:
- Time-saving ‘shortcuts.’
- Inadequate spending on training.
- Incomplete or improper training.
- Lack of safety officers on site.
- Poor housekeeping.
- Inexperienced workers.
Keep the above in mind when you review your Safety plan. Ask yourself what measures you can introduce to keep your team from stumbling down similar roads.
You’ll never be able to create and sustain the conditions for failsafe operations. Unfortunate events can slip through the cracks regardless of our efforts. Yet, optimising how you manage safety will unlock perks that make it all worthwhile.
The Perks Of A Safer Workplace
Other than the obvious (and most important) boon of a safe work environment – the well-being of your employees… The silver lining stretches far beyond that.
You can expect cuts in operational downtime, insurance costs and penalty fees. You can rest assured knowing you’re compliant with regulatory standards, and you’ll impart invaluable safety knowledge and experience to your team that could last a lifetime.
It All Starts With A Solid Warehouse Safety Plan
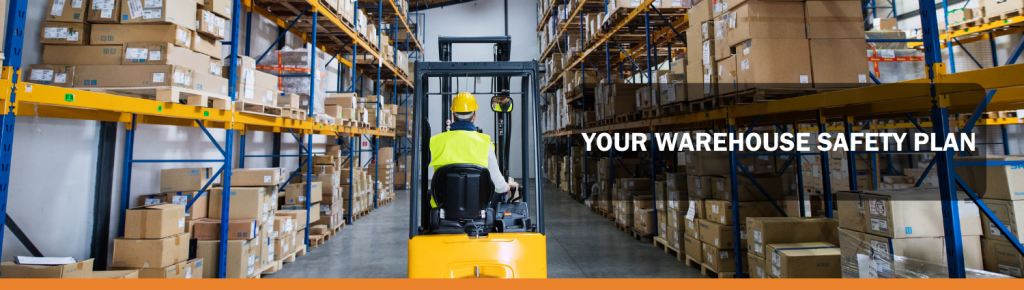
Your Warehouse Safety Plan (WSP) will serve as a map of proactive and reactive measures to circumvent risks that pose a threat to your employees and inventory.
Every section of your plan should include a purpose statement, the scope of practice, the people responsible and the procedures to follow in the given scenario.
Typically, you’d want to add all of the following sections to your plan:
1. Risk Assessments
At the bare minimum, warehouse risk assessments should be conducted at least once a year – or when key events (operational upgrades, infrastructural changes, equipment failure, employee injuries, etc. ) trigger the need for one.
This assessment involves the re-evaluation of the entire safety plan. Hazards are identified from scratch, and their ‘likelihood’ and ‘severity’ scores are re-calculated. This information is then used to inform a novel set of safety requirements.
2. Warehouse Safety Protocols
Written Safety Protocols or “Standard Operating Procedures” contain all the protective measures needed to satisfy the requirements you identified during the Risk Assessment stage.
These protocols should satisfy legislative safety requirements and consist of clear, easy-to-follow instructions.
As a rule, every component and process that contains any risk should have its own protocol.
Every protocol will contain the following:
- Selection Guidelines – A brief summary of the product/process specifications needed to get the job done effectively and safely.
- Operating procedures – Steps to follow for the safe execution of a specific task.
- Maintenance and Inspection Schedules -Guidelines for maintaining equipment and performing quality inspections. It’s a good idea to include inspection checklists and schedules.
- Training Schedule -A summary of the training timeline relevant to this specific protocol and a brief overview of the program content.
- Certification Requirements – Stipulate all the requirements needed to perform certain tasks or operate specific equipment.
- Signage Guidelines – A list of instructions for the proper use of labels, boards and signs where hazards or risks have been identified in a specific scenario.
Here’s a useful pocketbook guide by OSHA called the “Worker Safety Series – Warehousing”, if you’re interested.
3. Emergency Response
This part of your plan should involve a lot of brainstorming.
Your list of emergency protocols shouldn’t be limited to your warehouse alone – it should account for your surroundings as well. You may have a chemical manufacturer close by. What do you plan to do when there’s a toxic spill?
This will take a lot of research, planning and collaboration, but once the blueprint exists – you’ll be glad you put in the effort.
Here are some emergency protocol tips:
- Have a certified first-aid worker close by with every high-risk operation.
- Have a copy of your emergency response plan easily accessible at all times.
- Stipulate the frequency of drills needed per annum for every emergency in your plan.
- Install communication systems and alarms.
- Keep emergency supplies on hand. The bare minima are fire extinguishers, first-aid kits and a visible list of emergency contacts.
- Designate assembly points and assign emergency roles to workers.
OSHA covers a lot of ground on emergency response and preparedness in this article.
4. Training & Certification
The training program is another critical component of a safety plan. You’ll need a detailed curriculum that covers every aspect of safety. The best programs contain a combination of internal and third-party training sessions – involving workshops, practical exercises, theoretical tests and drills.
Skill development and safety training initiatives go hand-in-hand. The more competent your workforce, the less they’ll tip-toe on the verge of error.
5. Reports & Investigation
You’ll need a sound system to keep regulatory reports and documentation well organised. Jot down the reporting frequency for each type of report, the workers responsible and the essential details you’ll need to capture.
Digital tools can be a massive help here. Expanding legislative and operational requirements may need frequent alteration to your reports, and digital forms are perfect for quick fixes that readily update across all devices.
Higher incident reporting rates are proven to be effective in accident prevention as well. We created a complete guide on Effective Incident Reporting – check it out.
6. Audits & Recordkeeping
Third-party inspectors conduct comprehensive safety audits with an element of surprise. They can show up unannounced at any time of the year, and you’ll sleep better at night knowing you’re prepared.
The nature of your operations primarily determines the frequency of these audits. Schedule an internal audit or two just to play it safe. These will serve as mock tests to ensure compliance when the real deal arrives.
As for record-keeping, different documents have different time requirements. Injury reports must be kept for at least five years, while training records must be kept for three, for example.
We strongly advise you to store all your documents on the cloud (OSHA approves😉.) This way, your forms can be easily retrieved and managed from anywhere at any time.
Tips To Achieve Optimal Warehouse Safety Standards
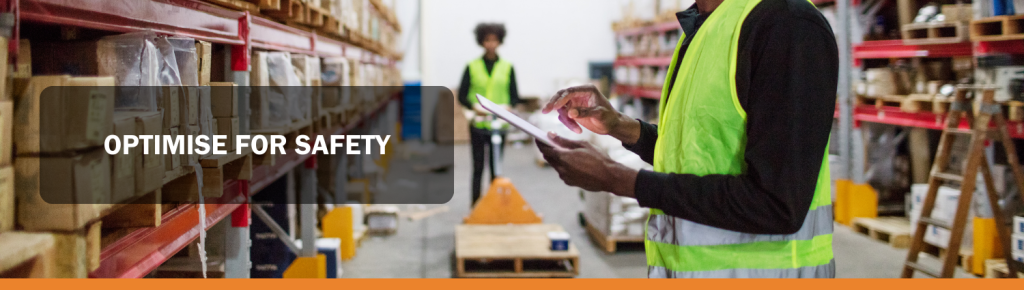
1. Utilise Real-time Data
Identifying hazards is one thing, but instantly triggering awareness across an entire workforce can be tricky.
Luckily for us, modern tools make this simple.
At the very least, CCTV camera systems can help to monitor operations in real time, but you’ll need a watchful set of eyes (or two) behind the screens at all times.
Mobile form builders, like Appenate, can help you capture data (even when there’s no internet connection) that readily syncs with your database as soon as you’re connected again. Your entire team can stay on the same page and jump in to correct hazards quickly.
Finally, safety sensors are excellent at removing the burden of hazard detection from your workers. Zebra Technology has some of the best electronic temperature monitoring and sensing solutions on the market.
2. Cultivate A Safety-First Culture
The best system out there can’t compensate for a negligent or indifferent workforce. You’ll need to instil genuine awareness and concern regarding safety issues in your warehouse.
Training is a necessary starting point, but you must humanise the process to establish a living and positive safety culture. Here’s how.
A. Lead From The Top Down
If your Managers, safety officers and supervisors reflect a genuine concern about safety in the workplace, that sentiment will often cascade downward.
B. Positive Reinforcement
Recognition works wonders. Consider thanking employees for reporting efforts in meetings or keep a point-scoring board where specific scores unlock leave or gift-card incentives.
C. Visual Reminders
Pitch a few posters here and there to prompt situational awareness.
D. Encourage Workers To Speak Up
Employees are often intimidated by the idea of sharing, so an openly-available box of suggestions can make them more comfortable with the experience.
Here’s a thought-provoking video by SW MGT with questions to ask yourself if you’d like to improve the way you lead safety initiatives.
3. Embrace Ergonomic Solutions
The cost of compensating workers for strain-based injuries can quickly add up, not to mention the risks of having high-value employees bedridden for days or even months. Your employees give their best when they’re taken care of.
Be sure to add an entire section on ergonomic factors in your Warehouse Safety Plan. Include best practices, equipment handling advice and a symptomology list for the early detection of strains.
We recommend you browse over this dedicated ‘Ergonomics’ article by OSHA.
Here are a few other things you can do to prevent employee strain:
- Invest in equipment and machines that are ergonomically designed.
- Utilise posters with posture and handling guidelines.
- Allow regular breaks and rotate tasks more frequently.
- Ensure all areas are adequately lit and invest in anti-glare screens to prevent eye strain.
Your Next Step?

Once your WSP is in check, go on and tend to operational improvements. An efficient reporting system is one of the best ways to raise the bar on all fronts.
Many companies trust our platform to help them comply with regulatory safety standards.
We provide the software they need to create custom digital forms, and they get to roll out a fully integrated, offline-capable and mobile solution in turn.
Check out this case study, where Appenate played a key role in obtaining ISO25001 certification for a client of KAS Consulting.
Sign up for our free trial and jump in to create all the safety reports you need with the help of our superb support team. You’ll get to create powerful apps (like these) with modern features that will transform the way you capture data for good.
If you’re still reading, we’d like to thank you for your commitment to a safer workplace. If you have any questions about Appenate, feel free to contact us at any time.
Stay safe🙂